Iso 12100-1:2003 機械の安全性-第1部: 基本用語,方法論 jis b9700-1 2004 isoは、iso12100-1、iso12100-2,及びiso14121-1の 3規格を統合し1つの規格として2010年に発行された規格である。 iso 12100-2:2003 機械の安全性-第2部: 技術原則 jis b9700-2 2004 iso14121-1.
Z432-16 - Safeguarding of machinery
Preface
This is the third edition of CSA Z432, Safeguarding of machinery. It supersedes the previous editions published in 2004 and 1994.This Standard specifies requirements for the design, manufacture (including remanufacture and rebuilding), installation, maintenance, operation, and safeguarding of industrial equipment to prevent injuries and accidents and enhance the safety of personnel who operate, assemble, and maintain machinery.
The scope of this new edition has been expanded to incorporate new international Standards on machinery design and performance and to provide additional information for the identification of hazards, including non-mechanical hazard(s). It contains the methodology for performing a comprehensive risk assessment. As indicated in Clause 4, this Standard is intended to be applied to newly manufactured, rebuilt, and redeployed machinery. However, it may also be used to set upgrade targets for existing machinery. This Standard provides advice on the basic principles of safeguarding and safety control performance to the extent that a manufacturing engineer, plant engineer, manager, or safety manager may interpret the advice and apply it to any particular machine. Additional illustrations are used to demonstrate the general application of these principles, although alternative safeguarding solutions may be equally effective.
The need for a new edition was prompted by the changing technology related to these machines and the wish of stakeholders, including regulators, employers, manufacturers, and labour, for a document that would reflect the latest thinking concerning operator and equipment safety. It was the intent of the Technical Committee to harmonize, where possible and where appropriate, with international Standards. For that reason, parts of this Standard are based on the latest editions of ISO 12100 and ISO 13849. Clauses 6.1 to 6.2.7, 6.2.9 to 6.3.4.1, 6.3.4.3, 6.3.4.4, and 6.3.5 to 6.4.5.3 are reproduced from ISO 12100 with permission.
The major changes to this edition include the following:
a) this Standard has been updated to harmonize with the latest ISO standards;
b) additional Annex material has been added to provide additional guidance and information for users;
c) Clause 5 on risk assessment has been significantly expanded and, where possible, harmonized with CAN/CSA-Z1002; and
Iso 12100 1 Pdf
d) allowable minimum (safe) distances have been changed to allow for the use of CAN/CSA-ISO 13857.CSA Group acknowledges that the development of this Standard was made possible, in part, by the financial support of federal, provincial, and territorial occupational health and safety government agencies.
Scope
1.1 GeneralThis Standard applies to the protection of workers from the hazards arising from the use of mobile or stationary machinery. It provides the criteria to be observed and the description, selection, and application of guards and protective devices. Where a current CSA Standard exists for a specific type of machinery (e.g., CSA B167, CAN/CSA-B354.2, CSA M424.1, CSA Z142, CAN/CSA-Z248, and CAN/CSA-Z434), it is to be used in conjunction with this Standard to provide the most effective protection.
En Iso 12100 Pdf
Note: This Standard is intended to be applied to newly manufactured and newly installed machinery as of the publication date of this Standard. The aim of this Standard is to promote a high standard of machinery safety during use.This Standard describes and illustrates a variety of protective measures and explains methods by which it is possible to assess which measure(s) it is reasonable to adopt in particular circumstances. As a minimum it will, however, be necessary to consult specific legislation in applying the principles set down. Although reference is made to specific types of machines, specific recommendations are not given for every type of machine. This Standard applies to rebuilt or redeployed machinery. The Standard can be used for enhancing the safety of existing machinery.
Iso 12100 Checklist Filetype:pdf
1.2 Exclusions
This Standard does not apply to portable hand tools.
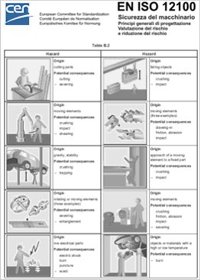
1.3 Purpose
This Standard is intended for those who design, build, modify, install, use, operate, or maintain machinery, machinery guarding, or protective devices. It is also intended to be used by those concerned with information for use of the machinery and the development and implementation of instructions, and training and the effective implementation of administrative controls.
1.4 Interaction with other standards
Machinery safeguarding is not performed in isolation from other protective measures. Typically, industrial machinery is installed in workplaces where other associated activities take place (e.g., movement of materials, cables, pipes, and hoses supplying energy, gases, and liquids, and workers on foot and operating vehicles). Other machinery and work environment standards applicable to any place where this Standard is being implemented should therefore be reviewed.
1.5 Terminology
In this Standard, shall is used to express a requirement, i.e., a provision that the user is obliged to satisfy in order to comply with the Standard; should is used to express a recommendation or that which is advised but not required; and may is used to express an option or that which is permissible within the limits of the Standard.
Notes accompanying clauses do not include requirements or alternative requirements; the purpose of a note accompanying a clause is to separate from the text explanatory or informative material.
Notes to tables and figures are considered part of the table or figure and may be written as requirements.
Annexes are designated normative (mandatory) or informative (non-mandatory) to define their application.
1.6 Measurements
The values given in SI units are the units of record for the purposes of this Standard. The values given in parentheses are for information and comparison only.
Content Provider
CSA America, Inc. [CSA]
Your Alert Profile lists the documents that will be monitored. If the document is revised or amended, you will be notified by email. You may delete a document from your Alert Profile at any time. To add a document to your Profile Alert, search for the document and click “alert me”.
Please first verify your email before subscribing to alerts.Your Alert Profile lists the documents that will be monitored. If the document is revised or amended, you will be notified by email. You may delete a document from your Alert Profile at any time. To add a document to your Profile Alert, search for the document and click “alert me”.
Already Subscribed to this document.Your Alert Profile lists the documents that will be monitored. If the document is revised or amended, you will be notified by email. You may delete a document from your Alert Profile at any time. To add a document to your Profile Alert, search for the document and click “alert me”.
A cobot, or collaborative robot, is a robot intended for direct human robot interaction within a shared space, or where humans and robots are in close proximity. Cobot applications contrast with traditional industrial robot applications in which robots are isolated from human contact.[1]Cobot safety may rely on lightweight construction materials, rounded edges, and inherent limitation of speed and force, or on sensors and software that ensures safe behavior.[2][3]
The International Federation of Robotics (IFR),[4] a global industry association of robot manufacturers and national robot associations, recognizes two types of robots – 1)industrial robots used in automation (in an industrial environment) and 2) service robots for domestic and professional use. Service robots could be considered to be cobots as they are intended to work alongside humans. Industrial robots have traditionally worked separately from humans behind fences or other protective barriers, but cobots remove that separation.
Cobots can have many uses, from information robots in public spaces (an example of service robots),[5] logistics robots that transport materials within a building,[6] to industrial robots that help automate unergonomic tasks such as helping people moving heavy parts, or machine feeding or assembly operations.
The IFR defines four levels of collaboration between industrial robots and human workers:[7]
- Coexistence: Human and robot work alongside each other without a fence, but with no shared workspace.
- Sequential Collaboration: Human and robot are active in shared workspace but their motions are sequential; they do not work on a part at the same time.
- Cooperation: Robot and human work on the same part at the same time, with both in motion.
- Responsive Collaboration: The robot responds in real-time to movement of the human worker.
In most industrial applications of cobots today, the cobot and human worker share the same space but complete tasks independently or sequentially (Co-existence or Sequential Collaboration.) Co-operation or Responsive Collaboration are presently less common.
History[edit]
Cobots were invented in 1996 by J. Edward Colgate and Michael Peshkin,[8] professors at Northwestern University.Their 1997 US patent entitled 'Cobots' [9] describes 'an apparatus and method for direct physical interaction between a person and a general purpose manipulator controlled by a computer.'The invention resulted from a 1994 General Motors initiative led by Prasad Akella of the GM Robotics Center and a 1995 General Motors Foundation research grant intended to find a way to make robots or robot-like equipment safe enough to team with people.[10] The first cobots assured human safety by having no internal source of motive power. Instead, motive power was provided by the human worker.[11]The cobot's function was to allow computer control of motion, by redirecting or steering a payload, in a cooperative way with the human worker. Later cobots provided limited amounts of motive power as well.[12] General Motors and an industry working group used the term Intelligent Assist Device (IAD) as an alternative to cobot, which was viewed as too closely associated with the company Cobotics. At the time, the market demand for Intelligent Assist Devices and the safety standard 'T15.1 Intelligent Assist Devices - Personnel Safety Requirements'[13] was to improve industrial material handling and automotive assembly operations.[14]
Cobotics,[15] a company founded in 1997 by Colgate and Peshkin, produced several cobot models used in automobile final assembly[16][12] These cobots were of IFR type Responsive Collaboration using what is now called 'Hand Guided Control'. The company was acquired in 2003 by Stanley Assembly Technologies.
KUKA released its first cobot, LBR 3, in 2004. This computer controlled lightweight robot was the result of a long collaboration with the German Aerospace Center institute.[17] KUKA further refined the technology, releasing the KUKA LBR 4 in 2008 and the KUKA LBR iiwa in 2013.[18]
Universal Robots released its first cobot, the UR5, in 2008.[19] In 2012 the UR10 cobot[20] was released, and later a smaller, lower payload UR3 in 2015. Rethink Robotics released an industrial cobot, Baxter, in 2012[21] and smaller, faster collaborative robot Sawyer in 2015, designed for high precision tasks.
FANUC[22] released its first collaborative robot in 2015 - the FANUC CR-35iA with a heavy 35kg payload.[23] Since that time FANUC has released a smaller line of collaborative robots including the FANUC CR-4iA, CR-7iA and the CR-7/L long arm version.
ABB released in 2015 YuMi,[24] the first collaborative dual arm robot.
As of 2019 Universal Robots was the market leader followed by Techman Robot Inc..[25]
Standards and guidelines[edit]
RIA BSR/T15.1, a draft safety standard for Intelligent Assist Devices, was published by the Robotic Industries Association, an industry working group in March 2002.[26]
The robot safety standard (ANSI/RIA R15.06 was first published in 1986, after 4 years of development. It was updated with newer editions in 1992 and 1999. In 2011, ANSI/RIA R15.06 was updated again and is now a national adoption of the combined ISO 10218-1 and ISO 10218-2 safety standards. The ISO standards are based on ANSI/RIA R15.06-1999. A companion document was developed by ISO TC299 WG3 and published as an ISO Technical Specification, ISO/TS 15066:2016. This Technical Specification covers collaborative robotics - requirements of robots and the integrated applications.[27] ISO 10218-1 [28] contains the requirements for robots - including those with optional capabilities to enable collaborative applications. ISO 10218-2:2011 [29] and ISO/TS 15066[30] contain the safety requirements for both collaborative and non-collaborative robot applications. Technically, the <collaborative> robot application includes the robot, end-effector (mounted to the robot arm or manipulator to perform tasks which can include manipulating or handling objects) and the workpiece (if an object is handled).
The safety of a collaborative robot application is the issue since there is NO official term of 'cobot' (within robot standardization). Cobot is considered to be a sales or marketing term because 'collaborative' is determined by the application. For example, a robot wielding a cutting tool or a sharp workpiece would be hazardous to people. However the same robot sorting foam chips would likely be safe. Consequently, the risk assessment accomplished by the robot integrator addresses the intended application (use). ISO 10218 Parts 1 and 2 rely on risk assessment (according to ISO 12100). In Europe, the Machinery Directive is applicable, however the robot by itself is a partial machine. The robot system (robot with end-effector) and the robot application are considered complete machines.[31][32]
See also[edit]
- Air-Cobot, a collaborative mobile robot to inspect aircraft
- Institute for Occupational Safety and Health of the German Social Accident Insurance (IFA): Safe co-operation between human beings and robots (http://www.dguv.de/ifa%3B/fachinfos/kollaborierende-roboter/index-2.jsp)
- Cobot, manufactured by Universal Robots
References[edit]
Iso 12100 Pdf Download
- ^'I, Cobot: Future collaboration of man and machine'The Manufacturer (2015-11-15). Retrieved on 2016-01-19
- ^https://ifr.org/downloads/papers/IFR_Demystifying_Collaborative_Robots.pdf
- ^ISO 10218-1:2011, ISO 10218-2:2011, ISO/TS 15066:2015
- ^ifr.org
- ^https://www.youtube.com/watch?v=W-RKAjP1DtA.
- ^http://www.aethon.com/tug/tughealthcare/
- ^https://ifr.org/downloads/papers/IFR_Demystifying_Collaborative_Robots.pdf
- ^Van, Jon (December 11, 1996). 'Mechanical Advantage'. Chicago Tribune.
- ^'Cobots' US Patent 5,952,796
- ^Teresko, John (December 21, 2004). 'Here Come the Cobots!'. Industry Week.
- ^'Cobot architecture'. IEEE Transactions on Robotics and Automation. 17 (4). 2001.[dead link]
- ^ ab'A History of Collaborative Robots: From Intelligent Lift Assists to Cobots' Engineering.com, October 28, 2016
- ^Published March 2002 by the Robotic Industries Association
- ^'Cobots for the automobile assembly line' International Conference on Robotics and Automation, Detroit, MI, 1999, pp. 728-733
- ^'Stanley moves into materials handling with Cobotics acquisition'. Cranes Today. April 2, 2003.
- ^'Intelligent Assist Devices: Revolutionary Technology for Material Handling'(PDF). Archived from the original(PDF) on 2017-01-05. Retrieved 2016-05-29.
- ^'DLR Light-Weight Robot III'. Archived from the original on 2016-11-14. Retrieved 2016-09-16.
- ^'History of the DLR LWR'. 2018-03-17.
- ^'A Brief History of Collaborative Robots' Engineering.com, May 19, 2016
- ^'UR10 Collaborative industrial robotic arm - Payload up to 10 kg'. www.universal-robots.com.
- ^'Baxter Kinematic Modeling, Validation and Reconfigurable Representation' SAE Technical Paper 2016-01-0334, 2016
- ^'FANUC Announces Record-Breaking 400,000 Robots Sold Worldwide'. FANUC America Corporation. Retrieved 2017-02-03.[permanent dead link]
- ^'FANUC America Introduces New CR-35iA Collaborative Robot Designed to Work Alongside Humans'. FANUC America Corporation. Retrieved 2017-02-03.[permanent dead link]
- ^'ABB Historical milestones'. Retrieved 2019-08-29.
- ^Huang, Elaine. 'This Made-in-Taiwan Robot Is Drawing International Attention'. english.cw.com.tw. CommonWealth. Retrieved 8 July 2020.
- ^Robotic Industries Association, BSR/T15.1 March 2020
- ^'ISO/TS 15066:2016 - Robots and robotic devices -- Collaborative robots'. www.iso.org.
- ^ISO 10218-1:2011 Robots and robotic devices – Safety requirements for industrial robots – Part 1: Robots. International Organization for Standardization (ISO)
- ^ISO 10218-2:2011 Robots and robotic devices – Safety requirements for industrial robots – Part 2: Robot systems and integration. International Organization for Standardization (ISO)
- ^ISO/TS 15066:2016 Robots and robotic devices – Collaborative robots. International Organization for Standardization (ISO)
- ^Machinery Directive
- ^Guide to the Machinery Directive